0 引言
1 实验装置与方法
1.1 实验装置
Fig. 1 Schematic of the experimental system图1 实验系统结构图 |
1.2 实验方法
Table 1 Parameters of the experimental oil samples表1 实验组油液样本参数 |
使用铁粉规格/目 | 组别 | 磨粒质量浓度/(mg/mL) |
---|---|---|
100 | 1-1 | 0.137 |
1-2 | 1.352 | |
200 | 2-1 | 0.164 |
2-2 | 0.165 | |
2-3 | 0.625 | |
2-4 | 0.787 | |
300 | 3-1 | 0.048 |
3-2 | 0.091 | |
3-3 | 0.138 | |
3-4 | 0.184 | |
3-5 | 0.228 | |
3-6 | 0.268 | |
3-7 | 0.313 | |
3-8 | 0.359 | |
3-9 | 0.408 | |
3-10 | 0.454 | |
500 | 4-1 | 0.016 |
4-2 | 0.031 | |
4-3 | 0.048 | |
4-4 | 0.063 | |
4-5 | 0.078 | |
4-6 | 0.094 | |
1 000 | 5-1 | 0.008 |
5-2 | 0.015 | |
5-3 | 0.020 | |
5-4 | 0.033 |
1.3 数据处理
Fig. 2 Flowchart of hologram processing图2 全息图处理流程 |

Fig. 3 (a) Raw hologram; (b) depth-of-field extended image; (c) binary image; (d) 3D distribution of wear particles in the measurement volume图3 (a)原始全息图;(b)景深拓展图;(c)二值化图像;(d)磨粒在测量体积内的三维分布 |
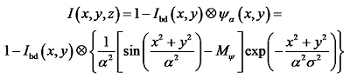




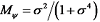

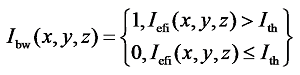


2 实验结果与分析
2.1 粒度分布测量结果比较
Fig. 4 Comparison of particle size distributions measured by holographic method and laser particle size analyzer图4 全息测量与激光粒度仪测量的粒度分布对比 |
Table 2 Median diameter Dv50 and error analysis表2 中位径Dv50及误差分析 |
组别 | 实验组Dv50/μm | 对照组Dv50/μm | 绝对误差/ μm | 相对误差/ % |
---|---|---|---|---|
100目 | 199.69 | 211.40 | 11.71 | 5.54 |
200目 | 42.12 | 40.55 | 1.57 | 3.87 |
300目 | 41.65 | 39.75 | 1.90 | 4.78 |
500目 | 28.95 | 18.36 | 10.59 | 57.68 |
1 000目 | 30.04 | 18.39 | 11.65 | 63.34 |
2.2 磨粒浓度影响分析
Fig. 5 Comparison of cumulative particle size distribution curves between the sample 3-1 and 3-10图5 实验组3-1和3-10粒径累积分布曲线对比 |
Table 3 Results of parallel experiments of 300 mesh iron powder under similar wear particle concentration表3 相近磨粒浓度下300目铁粉平行实验测量结果 |
实验组号 | 实验次数 | 磨粒质量浓度/ (mg/mL) | Dv10/μm | Dv50/μm | Dv90/μm |
---|---|---|---|---|---|
1 | 1 | 0.187 | 19.83 | 38.57 | 59.90 |
2 | 0.180 | 21.92 | 39.20 | 59.00 | |
3 | 0.186 | 17.30 | 36.13 | 56.15 | |
2 | 1 | 0.313 | 19.24 | 37.20 | 56.18 |
2 | 0.308 | 18.86 | 37.02 | 60.91 | |
3 | 0.311 | 19.25 | 38.93 | 61.21 |
Fig. 6 Characteristic particle size variation diagram of samples 3-1 to 3-10图6 实验组3-1至3-10特征粒径变化图 |
2.3 磨粒形貌特征分析
Fig. 7 Morphology of wear particles图7 磨粒形貌 |
Table 4 Analysis of wear particle morphology characteristic parameters表4 磨粒形貌特征参数分析结果 |
磨粒 | 面积/μm2 | 长轴/μm | 短轴/μm | 圆形度 |
---|---|---|---|---|
颗粒1 | 3 769.00 | 91.98 | 54.38 | 0.81 |
颗粒2 | 6 943.36 | 95.59 | 92.70 | 0.96 |
颗粒3 | 1 778.00 | 135.92 | 22.04 | 0.26 |